Choose The Best Manufacturing Equipment For Your Business
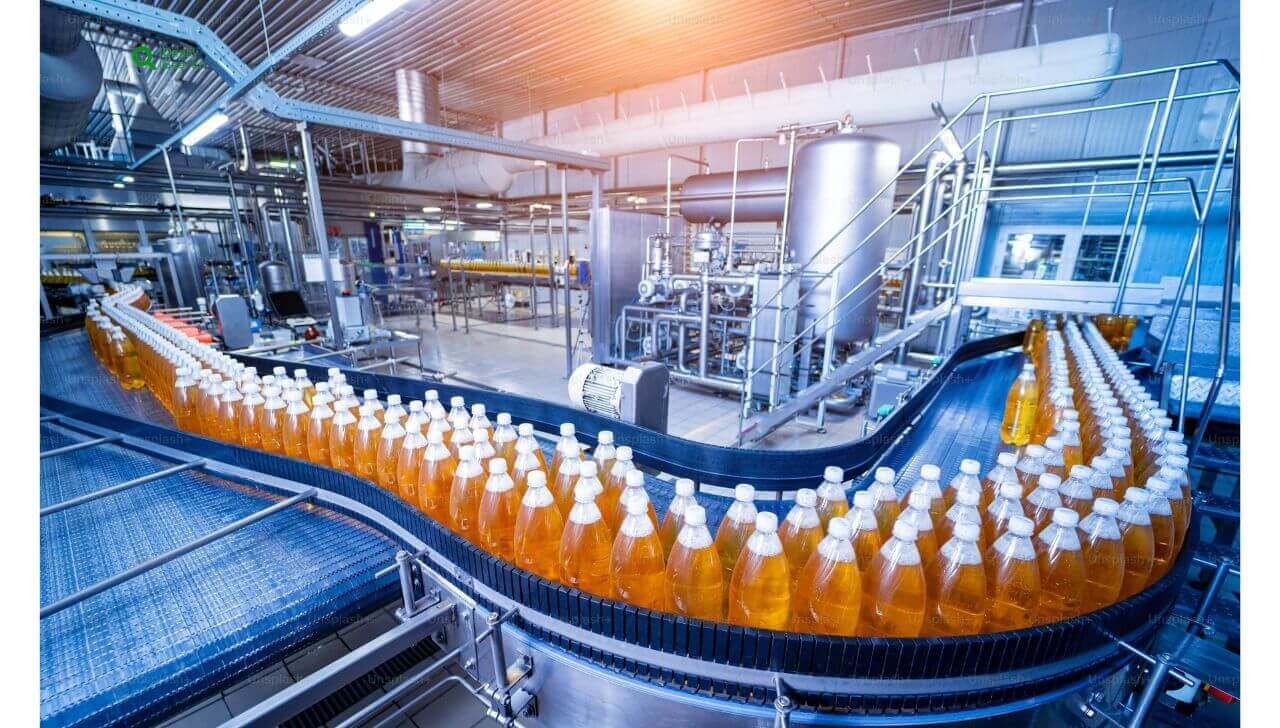
Manufacturing equipment plays a crucial role in modern industries, enabling businesses to produce goods efficiently, maintain quality, and reduce costs. From automated machinery to precision tools, the right equipment enhances productivity and ensures smooth operations. Whether you’re a small business or a large-scale manufacturer, investing in the right machinery can make all the difference.
Their presence is crucial in maintaining the cadency and quality of the manufacturing process, ensuring that manufacturing companies stay abreast of changing market demands. In this guide, we’ll explore different types of manufacturing equipment, their benefits, and how to choose the best options for your needs.
What is Manufacturing Equipment?
Manufacturing equipment is the foundation of production, facilitating the conversion of raw materials into completed products efficiently and precisely. This includes machines for cutting, molding, assembling, packaging, and quality control. Equipment ranges from basic hand tools to advanced automated systems that improve efficiency, precision, and productivity in industries like automotive, electronics, food processing, and textiles. Investing in the right equipment helps businesses streamline operations, reduce costs, and maintain high-quality standards.
Important of Manufacturing Equipment
Manufacturing equipment is essential for efficient production, quality control, and cost reduction in industries. It enhances productivity, ensures precision, and minimizes human errors. Advanced machinery enables automation, speeding up processes and reducing labor costs. Reliable equipment also improves workplace safety and maintains product consistency. Investing in the right manufacturing tools helps businesses stay competitive, meet market demands, and scale operations effectively.
Understanding Your Manufacturing Equipment Needs
Selecting the right manufacturing equipment is crucial for ensuring efficiency, quality, and cost-effectiveness in production. Whether you are starting a new manufacturing business or upgrading your current machinery, it is important to assess your specific needs carefully. Making informed decisions about equipment can help you maximize productivity, reduce downtime, and stay competitive in the industry. Below is a detailed guide to help you understand and evaluate your equipment needs.

Assess Your Production Requirements
The first step in selecting the right manufacturing equipment is to analyze your production requirements. Consider the type of products you are manufacturing, the expected production volume, and the level of precision needed. Understanding these factors will help you determine whether you need high-speed automated machinery or smaller-scale equipment that offers more flexibility. Additionally, consider industry standards and regulatory requirements to ensure your equipment meets all necessary compliance guidelines. A clear understanding of your production goals will help you make informed decisions when purchasing equipment.
Consider Automation and Technology
With advancements in technology, many manufacturing processes have shifted toward automation, improving efficiency and reducing labor costs. When evaluating equipment, consider whether a fully automated, semi-automated, or manual system best suits your operations. Smart manufacturing technology, such as AI-driven quality control systems and IoT-enabled monitoring, can enhance efficiency and accuracy. If your business is expected to scale in the future, it is beneficial to invest in equipment that allows for upgrades and integration with advanced technologies. Choosing machines that support automation and smart technology can streamline your operations and improve overall productivity.
Budget and Cost Analysis
Investing in manufacturing equipment requires careful financial planning. It is essential to balance the initial purchase cost with long-term benefits such as energy efficiency, reduced maintenance costs, and increased output. A high-quality machine may have a higher upfront cost but could save money in the long run by minimizing downtime and repair expenses. Additionally, factor in operational costs such as power consumption, labor expenses, and raw material usage. Exploring financing options, leasing alternatives, or government incentives for manufacturing investments can help you manage costs effectively while acquiring the necessary equipment.
Space and Facility Layout
Before purchasing new equipment, assess your facility’s available space and layout. Manufacturing equipment varies in size, and it is essential to ensure that your workspace can accommodate the machines without causing disruptions in workflow. Consider factors such as ventilation, power supply, and worker accessibility when planning equipment placement. A well-organized facility layout allows for smooth material flow, minimizes bottlenecks, and enhances overall efficiency. Proper spacing and ergonomic design also contribute to a safer work environment by reducing the risk of accidents and equipment malfunctions.
Vendor and Supplier Selection
Choosing a reliable vendor or supplier is just as important as selecting the right equipment. A trustworthy supplier provides high-quality machines, reliable after-sales support, and access to spare parts. Research different vendors, compare customer reviews, and assess their reputation in the industry. Consider working with manufacturers who offer warranties, technical training, and responsive customer service. Establishing a long-term partnership with a reliable supplier can ensure smooth equipment operation and minimize unexpected downtime due to faulty machinery or lack of spare parts.
Compliance with Safety and Regulations
Manufacturing equipment must comply with industry safety standards and regulatory requirements. Machines should be equipped with proper safety features such as emergency stop buttons, protective guards, and ventilation systems. In the U.S., for example, businesses must follow Occupational Safety and Health Administration (OSHA) regulations to ensure worker safety. Additionally, environmental regulations should be considered, particularly if your equipment produces emissions or industrial waste. Ensuring compliance not only protects workers but also prevents legal issues and penalties that could impact your business operations.
Future-Proofing Your Investment
As technology and market demands evolve, it is important to invest in equipment that remains relevant in the long term. Look for machines that offer upgrade options or modular components that allow for future expansion. Equipment that can adapt to different materials or production techniques provides greater flexibility and prevents obsolescence. Additionally, consider investing in smart manufacturing solutions that offer real-time data analytics, allowing you to monitor performance, identify inefficiencies, and optimize production processes. Future-proofing your investment ensures that your manufacturing facility remains competitive and adaptable to changing industry trends.
The Different Types of Manufacturing Equipment
Manufacturing equipment plays a vital role in transforming raw materials into finished products. Different types of machines serve specific functions in the production process, from cutting and shaping to assembling and packaging. Choosing the right equipment ensures efficiency, precision, and cost-effectiveness. Below are the major types of equipment used in various industries.
1. Material Handling Equipment: Material handling equipment is used to transport, store, and manage raw materials, work-in-progress, and finished goods within a manufacturing facility. This category includes conveyors, forklifts, cranes, and automated guided vehicles (AGVs). Conveyors move materials along a production line, reducing manual labor and increasing efficiency. Forklifts and cranes assist in lifting heavy materials, while AGVs provide automated transport solutions. Proper material handling equipment improves workflow, reduces downtime, and enhances workplace safety.
2. Cutting and Shaping Equipment: Cutting and shaping equipment is essential for modifying raw materials into specific forms and sizes. This category includes lathes, milling machines, laser cutters, water jet cutters, and CNC (Computer Numerical Control) machines. Lathes are used for shaping cylindrical materials, while milling machines create precise cuts on various surfaces. Laser and water jet cutters provide high-precision cutting for metals, plastics, and composites. CNC machines automate cutting and shaping processes, ensuring accuracy and consistency in mass production. These machines play a crucial role in industries such as automotive, aerospace, and metal fabrication.
3. Forming and Molding Equipment: Forming and molding equipment is used to shape materials into desired forms through processes such as bending, stamping, casting, and injection molding. Stamping presses are commonly used in metal fabrication to create complex shapes from sheet metal. Casting machines melt metal or plastic and pour it into molds to form intricate components. Injection molding machines are widely used in the plastics industry to produce mass-produced parts with high precision. These machines are crucial for manufacturing automotive parts, consumer goods, and medical devices.
4. Joining and Welding Equipment: Joining and welding equipment is used to assemble components by bonding materials together. Welding machines use heat to fuse metal parts, creating strong and durable joints. Common types of welding include MIG (Metal Inert Gas), TIG (Tungsten Inert Gas), and laser welding. Riveting machines and adhesive bonding equipment are alternative methods for joining materials without using heat. These machines are essential in industries such as construction, shipbuilding, and automotive manufacturing, where strong and reliable connections are required.
5. Machining Equipment: Machining equipment is used to refine materials by removing excess material and shaping them into precise components. This category includes drills, grinders, and precision machining tools such as CNC machining centers. Drilling machines create holes in materials, while grinders smooth surfaces for a polished finish. CNC machining centers automate complex machining tasks, ensuring high accuracy and repeatability. Machining equipment is widely used in industries that require high-precision parts, such as aerospace, medical device manufacturing, and automotive engineering.
6. Heat Treatment Equipment: Heat treatment equipment is used to alter the physical and chemical properties of materials through controlled heating and cooling processes. This category includes furnaces, ovens, and induction heating machines. Heat treatment processes such as annealing, hardening, tempering, and quenching improve material strength, durability, and resistance to wear. Industries such as metalworking, tool manufacturing, and aerospace rely on heat treatment equipment to enhance the performance of their products.
7. Assembly and Packaging Equipment: Assembly and packaging equipment streamlines the final stages of production by putting together components and preparing products for distribution. Automated assembly lines use robotic arms and conveyor systems to assemble products quickly and efficiently. Packaging machines include labeling machines, shrink-wrapping machines, and box-sealing machines that ensure products are securely packed for transportation. These machines are essential for industries such as consumer electronics, pharmaceuticals, and food processing, where high-speed and precise packaging is required.
8. Quality Control and Testing Equipment: Quality control and testing equipment ensure that manufactured products meet industry standards and customer expectations. This category includes coordinate measuring machines (CMM), vision inspection systems, and non-destructive testing (NDT) equipment. CMM machines measure the dimensions of components with extreme accuracy, while vision inspection systems use cameras and AI to detect defects. NDT methods such as ultrasonic, X-ray, and magnetic particle testing help identify internal flaws without damaging the product. High-quality control standards improve customer satisfaction and reduce product recalls.
9. Finishing Equipment: Finishing equipment is used to enhance the appearance and durability of products through processes such as painting, coating, and polishing. Spray painting machines apply paint or protective coatings evenly, while powder coating equipment provides a durable, corrosion-resistant finish. Polishing machines smooth surfaces to improve aesthetics and reduce friction. Finishing processes are commonly used in the automotive, furniture, and consumer goods industries to create visually appealing and long-lasting products.
10. Specialized Equipment: Some manufacturing processes require specialized equipment tailored to specific industries. For example, textile manufacturing machines such as looms and knitting machines produce fabrics, while food processing equipment such as mixers, blenders, and pasteurizers are designed for food production. Semiconductor manufacturing requires cleanroom-compatible machines for producing microchips. These specialized machines ensure that industry-specific requirements are met with high precision and efficiency.
Frequently Asked Question
Here are some frequently asked question about this topic:
What factors should I consider when choosing manufacturing equipment?
When selecting manufacturing equipment, consider factors such as production volume, material type, automation level, energy efficiency, maintenance requirements, and budget. It’s also important to evaluate the scalability of the equipment to ensure it meets future business growth.
How often should manufacturing equipment be maintained?
Maintenance schedules depend on the type of equipment and usage frequency. Generally, routine maintenance should be performed weekly or monthly, while preventive maintenance, such as lubrication and part replacements, should be done quarterly or annually. Regular maintenance helps prevent breakdowns and extends equipment lifespan.
What are the benefits of automation in manufacturing equipment?
Automated manufacturing equipment improves efficiency, reduces human errors, enhances product consistency, and lowers labor costs. It also increases production speed and ensures better quality control, leading to higher profitability and reduced waste.
How can I improve the lifespan of my manufacturing equipment?
To extend the lifespan of manufacturing equipment, follow proper maintenance schedules, use high-quality spare parts, train employees on correct operation, and ensure proper storage and cleaning. Regular inspections and timely repairs prevent major issues and costly downtime.
What safety measures should be taken when operating manufacturing equipment?
Operators should follow safety protocols such as wearing personal protective equipment (PPE), adhering to machine operating guidelines, using emergency stop functions when necessary, and undergoing proper training. Equipment should also comply with workplace safety standards such as OSHA regulations to prevent accidents.
Conclusion
Manufacturing equipment plays a vital role in modern industrial production, driving efficiency, quality, and cost-effectiveness. By automating processes, improving precision, and enhancing workplace safety, businesses can achieve higher productivity while minimizing waste and operational costs. Advanced machinery also provides scalability and flexibility, allowing companies to adapt to changing market demands.
Investing in high-quality manufacturing equipment is essential for maintaining a competitive edge, ensuring consistent product quality, and achieving long-term business growth. As technology continues to evolve, integrating smart manufacturing solutions will further optimize production processes and enhance overall efficiency.